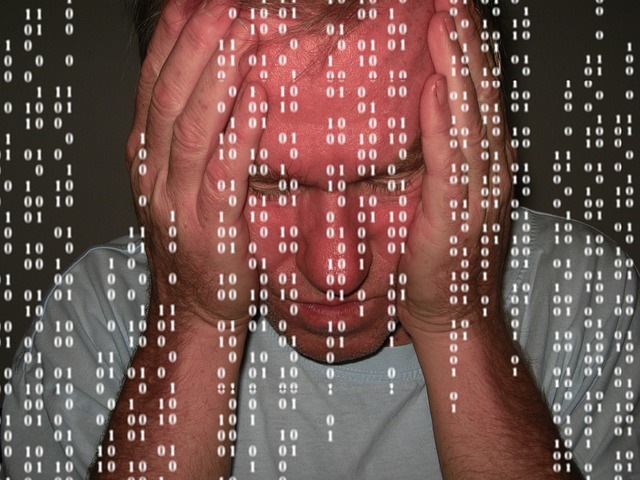
Are you sure, that you’re sure, that your gas compliance data is accurate?
We all know that failure to comply with gas safety standards, and regulations, can pose serious risks to social housing customers, including the potential for gas leaks, fires, or carbon monoxide poisoning. Regular maintenance of gas appliances is an essential part of the role as landlord.
Landlords will all have robust maintenance schedules, replacement programs, suitable repair priorities, policies, and procedures to make sure they fulfil their obligations to keep their customers safe in their home. So why, when they are so aware and focussed on this aspect of their work, do mistakes happen?
Lack of communication with customers
One of the obligations is to communicate well with customers enabling them to also keep themselves safe. For example:
- Explaining that adequate ventilation is crucial to prevent the build-up of harmful gases where there are gas appliances such as their boiler, or their fire.
- How to recognise the signs of a gas leak, and what to do if they suspect a leak.
- Giving them information on how to use gas appliances safely.
- How to report gas appliance issues promptly.
- The importance of allowing the landlord access for routine servicing.
All too often these aspects of safety knowledge are left unsaid, or are assumed.
Data issues
3C have worked with multiple housing organisations to quality check and assure their compliance data across all six compliance areas: Fire, Lift, Asbestos, Gas, Electric and Legionella (aka FLAGEL).
Not unsurprisingly, gas compliance data is often the area we are asked to initially focus on. Our customers have ranged from those who already believe they are 100% compliant (or very close) to those who have doubt and want assurance.
Surprisingly however, none of the customers we have worked with have had the data to support their 100% (or close) claim. The reason is fundamentally one of two things:
- The data is incorrect; or
- The data is correct and their policies, procedures, training and/or data quality checking is inadequate.
It is vital that we understand which of these is the case so that the issues can be resolved. The way we approach this is to do in-depth quality checking of all of the related property and gas compliance data to establish what needs to change for the organisation’s leaders to have 100% assurance in the figures reported.
Data quality checking
We find that existing data quality checking, if any is in place, has focussed on the fundamentals and not explored all the possibilities. For example, asking the question “Does each property on the gas servicing schedule have a current gas safety certificate?” and not ensuring that a certificate, if it is in place, is dated within a particular date range. Of course, day by day the answer to this question will vary as time moves on and certificates expire, so monitoring needs to be automatically scheduled to happen on an ongoing basis and not considered an occasional exercise.
Examples of further checks can include:
- Checking properties that the organisation think should have a service against service jobs raised, and the corresponding certificates received.
- Checking that the date on the certificates received correspond to the service job date.
- Checking that the certificates received are identified as having gas components on the housing management and/or asset management system.
- Checking that the housing management system/asset management system properties that are marked as being compliant (using dates) have a corresponding certificate.
- Checking for certificates that are dated in the future.
- Checking for properties that have a heating type of gas but no service scheduled.
- Checking for properties that have no form of heating identified.
It is also vital that data quality checks are built and scheduled regularly. Even when this is the case, there is often systemic issues insofar as monitoring that the quality of the data is improving is not a focussed activity. The consequences of missing just one service, of one gas appliance, can be devastating.
Findings
Across the many organisations we have worked with, below are some examples of our findings:
- 66 properties with gas appliances but no carbon monoxide alarm.
- 41 properties with gas components and no service ever being undertaken.
- 130 properties where the number of gas appliances, and locations, did not match the number of carbon monoxide alarms.
- 638 properties where the service next due date had expired or was invalid.
- 48 properties with no heat source.
- 100 properties with incorrect servicing cycles.
- 3 service completion dates in the future.
- Multiple instances of data being held in more than one place and inconsistencies between data stores (including spreadsheets!)
Tools
We use a combination of our own internal expertise and our data quality and compliance tool, 3C Data Logic to deliver our data quality assurance service.
3C data consultants have experience of working in housing organisations at operational, management and executive levels. This means that we can bring sector knowledge and understanding to our service delivery and understand the nuances that different housing providers may have in their procedures and policies.
This knowledge, combined with our technological tool, 3C Data Logic, delivers a fully rounded and comprehensive data service to the sector.
More details on the data services we can provide can be found here.
3C Data Logic is a comprehensive data management tool – more details can be found here.